THE FUTURE OF COMMERCIAL MARIJUANA CULTIVATION
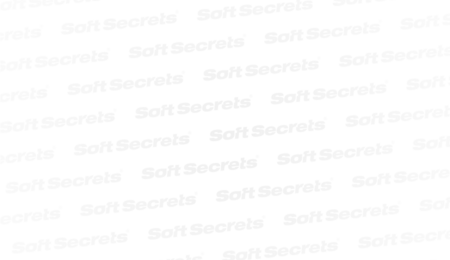
The Netherlands has cold, moist weather, poor quality soil, and river water high in dissolved solids after traversing Switzerland and Germany.
The Netherlands has cold, moist weather, poor quality soil, and river water high in dissolved solids after traversing Switzerland and Germany.
The Netherlands has cold, moist weather, poor quality soil, and river water high in dissolved solids after traversing Switzerland and Germany. It has a small landmass, high land and labor costs and is urban; yet, in monetary value, it is one of the world’s largest agricultural exporters.
This has come about through the cooperation of agricultural research universities, government-sponsored research at centers such as in Ede Wageningen, farmers, and manufacturers of agricultural equipment.
Seeding machine. A seed is inserted into each plug as the tray moves along the conveyor. Every plug receives a seed at a uniform depth. This machine handles hundreds of trays per hour.
The Netherlands boasts about 10,500 hectares of greenhouses.* These are used to grow vegetable crops, potted plants, cut flowers and ornamental bulbs. All of these are high-value crops so the return on the space is high. Other factors that keep the industry competitive are economies of scale and automation.
Greenhouses range in size from about one-half hectare to about 10 hectares. The average size is one and a half hectares. However, the trend is towards larger greenhouses and this is where much of the cutting-edge technology is used.
I recently took a tour of some commercial greenhouses in the Netherlands and of some of the controls and machinery factories where the equipment is manufactured.
However, before we look inside the Netherland greenhouses, let’s think about “large-scale” indoor gardens in the United States. Most of them have between 20 and 100 lights. I’ve seen a number of gardens in which the grower started with 20 to 30 lights. When the grower wanted to expand, s/he built out another space duplicating the first one several times, each time with some modifications. While these might be profitable and the changes lead to higher efficiency, these are market gardens. Although commercial, these small units and spaces usually cannot utilize appropriate technology like that used in larger spaces. It is the difference between gardening and farming.
Biological pest control. Here parasitoids are being released against aphids.
While the garden technique is profitable and requires only a nominal investment of €760 to €1,150 a light, it has very high operating costs consisting of energy and labor. Using farming techniques, growers can get as high a quality by lowering both costs. The cost of controls and machinery will initially be much higher, but there will be a fast return on the investment.
Until recently, U.S. growers had no incentive to invest in machinery or turn their gardens into farms. The threat of government interference was enough to stymie investment. However, the tide seems to have turned.
California NORML held a regional conference last January at Fort Mason, an urban National Park in San Francisco. Attendees celebrated the Washington and Colorado initiative victories that legalized marijuana for anyone over 21 years old. Time was spent developing a consensus for a 2016 legalization initiative in California. However, when I looked around, there were few young people in the crowd and there was a lot of grey hair, belonging to the formerly young activists.
Close-up of seedling-sorter claws.
It might be fitting that many of the same people who started the movement in the late 20th century plan to complete their tasks during the next presidential election cycle. The consensus is (and I agree with it), that: The upcoming initiative will be well worded, well funded, and most importantly, successful. Another cause for optimism is that the oldest 12 percent of the 2010 voters, those who were the most anti-legalization, will have passed on. New voters who are more likely to vote pro-pot are replacing them.
The next day after NORML’s regional conference, the NCIA, (National Cannabis Industry Association) held a meeting in Seattle, Washington. Both the entrepreneurs and the investors were a far younger group of people than attended the NORML conference. This seemed fitting too. This was the second surge. They were building on the activists’ foundation.
Net LEDs are hung between rows of hanging tomatoes in greenhouses so lower vegetation gets more light.
I had the feeling that this younger group, rather than many of the people already gardening, will create the cultivation transition. They are very business-minded, open to new ideas and technology and, although passionate about cannabis, they don’t have the same romance and wonder, the same intimacy with individual cannabis plants that is typical among gardeners.
It seems apparent that legalization will spur consolidation and that larger operations will result. Employing appropriate technology not generally useful in gardens will reduce growing costs. Dutch tools will play a major roll in the change from gardening to farming in the United States.
The new developments do not spell the end of market gardening. In Marijuana Grower’s Handbook I described the Tomato Model:
CleanLights are available in a hobby model in the United States.
Every size organization is involved in commercial tomato production— international corporations, large farmers who market nationwide, local farmers, and market gardeners. Yet home gardeners grow most tomatoes in the U.S. Washington State’s law does not allow personal cultivation. But this is not likely to deter home-growers.
The two most expensive operating costs of cultivation are labor and power for light and climate control. With legalization both those costs will be reduced.
Employment in the medical marijuana industry has always paid a steep premium over the same class of employment in other industries. This is the result of the inherent risks created by the current legal situation. As these risks decrease the premium will follow.
With less risk many people who have hesitated to work in a garden or dispensary will no longer be inhibited, so there will be a larger pool of potential employees, which also tends to push wages down.
Floating trays are used for short-season crops. Sea of green marijuana beds could use this method and the plants could easily be grown using this technique in these units.
The key to the Netherland’s success at farming as far as labor is concerned is not to push wages down, but to run extremely efficient operations in which most labor is performed by specialized machinery or with tools that increase worker efficiency.
Light is another matter. The weather in the Netherlands is cool and damp. It’s at latitude 52, the same as Quebec and some Alaskan islands. During the summer the days are long, but it’s overcast much of the time. Even when it’s sunny the light isn’t intense. Winter brings very short days and weak sunlight.
Even so, sunlight powers most photosynthesis and electric light is used to supplement it. Controls determine either the amount (intensity) of light being delivered or the Daily Light Interval (DLI), which keeps a count of how much light has been delivered during the day, a sort of meter for light similar to an odometer for distance. Controllers use these measurements to turn lights on and off.
If there are considerable savings in the Netherlands using natural light for plant growth, consider the U.S. state of Colorado. The state receives 300 days of sun each year and, because of altitude, it gets a bright light, so supplemental lighting would not be used as much. It will be hard for an all-electric grow room to compete with free power. So there will be a switch among serious commercial growers to sunlit systems. Colorado is just an example. From Florida to Maine, the cost of production is much lower when sunlight factors into the equation.
Filling machine for large containers eliminates a laborious task. Thousands of containers can be filled per hour.
Cogeneration systems may be feasible for some large greenhouses. Propane is burned to power a generator. The exhaust gas, primarily CO2, is collected and compressed for use later or used directly in the greenhouse during the lit periods. So the fuel is used to power a generator, heat the greenhouse and supply it with CO2. This cuts power costs further.
AUTOMATION
Every part of the cultivation, harvesting and manicuring process can be automated. Tools to speed pot-filling, planting, fertilizer injection, transplanting, pruning, pest control, moving plants, cutting, manicuring, drying, and packaging will decrease the amount of labor required to produce a finished bud or other marijuana product.
Most of the technology I saw on my last trip to the Netherlands was geared towards larger operations. But simpler versions are available. They are not quite as automated but are appropriate for a space of a quarter hectare and up. Some are portable so a rental business might be possible.
Adopting modern agricultural technology for marijuana will result in more uniform higher-quality produce because the plants will be quantified and provided for all the time without the vagaries that often accompany manual production. This will also result in lower production costs and more efficient use of resources.
*Total Area of the Netherlands is about 33,700 square kilometers as compared to the United States, roughly 9,800,000 square kilometers