Solvent-Free Electrostatic Trichome Separation
.jpg)
The global cannabis industry, valued in tens of billions of dollars, is locked in a constant battle for purity and quality. Modern consumers demand sophisticated products with precise cannabinoid and terpene profiles, while medicinal markets require strict pharmaceutical standards. For decades, producers have relied on traditional extraction methods that resemble brute-force artisanal techniques more than the scientific precision demanded by a mature industry.
These conventional processes, from ice water baths to aggressive mechanical sieving, frequently degrade the delicate phytochemical profile of the final product, sacrificing quality for quantity. Loss of volatile terpenes, contamination with pulverized plant material, and physical damage to glandular structures have been the price paid for decades of inadequate methods.
However, a truly revolutionary innovation is set to transform this paradigm forever. A groundbreaking study published in the prestigious Journal of Cannabis Research by Sambo Creeck experts Charles MacGowan and Alex Martynenko presents a solution as elegant as it is effective: electrostatic separation. This technology promises extracts of unprecedented purity while being completely sustainable, infinitely scalable, and extraordinarily respectful of the plant’s molecular integrity. The future of cannabis extraction does not lie in aggressive chemistry of the past but in the fundamental physical principles of static electricity.
The Achilles' Heel of a Booming Industry
To understand the magnitude of this breakthrough, it is essential to know exactly what is being extracted. The true magic of cannabis lies in tiny mushroom-shaped glandular structures called trichomes, concentrated primarily on female flowers. These microscopic factories, visible as a crystalline frost coating the buds, are solely responsible for producing and storing the plant’s vast natural pharmacy: cannabinoids like THC and CBD, aromatic terpenes defining flavor and effects, antioxidant flavonoids, and dozens of other bioactive compounds. A high-quality extract is essentially an ultra-concentrated collection of these precious trichome heads, completely free of any contaminating plant material such as chlorophyll, cellulose, or leaf fragments.
The technical challenge is separating these microscopic and extraordinarily delicate spheres from the rest of the plant biomass without destroying their structural integrity or altering their chemical content. Traditional methods face seemingly unsolvable systemic issues. Wet fractionation through agitation in ice water, though widely used, inevitably results in significant loss of water-soluble terpenes and requires slow, costly drying processes to prevent microbial contamination. Dry fractionation using vibrating screens is a precarious balancing act: aggressive processing maximizes yield but pulverizes plant matter, contaminating the final product; gentler processing preserves purity but sacrifices substantial amounts of valuable material. Both approaches are fundamentally unscalable for industrial production and heavily dependent on specialized labor.
The Elegant Solution: The Physics of Attraction
MacGowan and Martynenko approached the problem from a revolutionary angle. Instead of focusing on mechanical properties, they investigated the plant’s electrical characteristics using a Keithley 6517B electrometer under controlled conditions. Their discovery was simple yet profound: trichomes and plant biomass naturally carry opposite electrical charges. Trichomes have a net negative charge, while leaves and stems carry a positive charge.
This finding changed everything. Using this fundamental principle, they designed a free-fall electrostatic separator that uses intense electric fields to sort particles by charge. The concept is intuitive, similar to the classic school experiment where a charged comb attracts bits of paper. Here, the system meticulously separates the “gold” (trichomes) from the “dust” (plant material), but with industrial precision.
The process, commercialized as “Plasmastatic,” represents precision engineering:
⦁ Preparation and Charging: Ground, dry cannabis (74–220 microns) enters the system via a vibratory feeder. Pneumatically controlled airflow transports the material through a spiral tube, where triboelectric friction intensifies the natural opposite charges between trichomes and biomass. The turbulent flow prevents clumping.
⦁ Separation by Electric Field: Particles are injected through a narrow diffuser into a vertical chamber. They fall by gravity between non-parallel electrodes, generating electric fields of 10,000 volts per meter. This configuration creates stronger field gradients at the inlet for effective initial deflection.
⦁ Intelligent Collection: Negatively charged trichomes are attracted to the positive electrode, while positively charged biomass moves to the negative electrode. Neutral particles fall into a recycling bin. Self-cleaning electrodes with moving conductive belts allow for automated, continuous collection. This method is inherently gentle and non-destructive. It requires no violent agitation, harsh chemical baths, or extreme centrifugation that could damage cellular structures. The delicate heads of the trichomes are separated completely intact, preserving their valuable molecular contents without any chemical alteration.
Results: A Quantum Leap in Purity and Efficiency
The experimental figures are revolutionary. Traditional mechanical methods such as trommel drums achieve 40–60% initial purity, while Plasmastatic reaches 80–95% on the first pass. Multiple processing cycles deliver 98% total yield and up to 99.8% purity for specialized pharmaceutical applications.
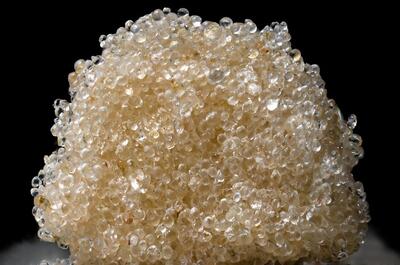
The benefits transform the industry. Being solvent-free, it eliminates environmental impact and chemical residues. It preserves trichome integrity and the full terpene profile. Its energy efficiency (approximately 20 watts for the prototype) enables integration with renewable energy sources. Modular scalability allows production from artisanal levels to over 100 kilograms per hour using parallel units.
Full automation with self-cleaning electrodes drastically reduces labor and operational costs. For a global industry urgently seeking industrial standardization and product consistency, this innovation represents the ultimate technological leap toward precision pharmaceutical manufacturing.
This revolutionary technology is no longer a future promise; it has been commercially available since 2023. Its rapid adoption marks the definitive historical shift from artisanal extraction to electrostatic industrial science, establishing new standards of purity and sustainability across medicinal and recreational cannabis markets worldwide.